Building a keyboard (part 5)
Strengthening the assembly and programming!
Now that I can start programming the keyboard, the first challenge was to get
the two halves to send joystick data across the wire. My initial approach was to
try adding code in matrix_scan_user
that directly performed actions based off
of the joystick pins, but this only works on the master side. By default, QMK
only sends the state of the matrix across the wire from the slave to the master,
so logic that sends reports to the host must only be performed on the master.
This led me down a mini rabbit hole where I tried to encode the joystick state as part of the matrix, but I couldn’t quite figure it out, which is just as well because I found what I really wanted - RPCs. QMK allows arbitrary RPC messages to be defined (with a modest maximum message size of 8 bytes) which allows the master to invoke a function on the slave and receive a response. Here’s the code I’m using:
typedef struct {
int x;
int y;
bool sw;
} joystick_state;
...
void get_local_joystick_state(joystick_state* out_data) {
out_data->x = analogReadPin(F0);
out_data->y = analogReadPin(F1);
out_data->sw = readPin(C7);
}
// Send data from the right half to the left
void get_joystick_state_handler(uint8_t in_buflen, const void* in_data, uint8_t out_buflen, void* out_data) {
// const rpc_req *req = (const rpc_req*)in_data;
get_local_joystick_state((joystick_state*)out_data);
}
void keyboard_post_init_user(void) {
transaction_register_rpc(RPC_GET_JOYSTICK_STATE, get_joystick_state_handler);
}
...
void matrix_scan_user(void) {
if (!is_keyboard_master()) {
return;
}
joystick_state new_left;
get_local_joystick_state(&new_left);
process_left_joystick(&new_left);
joystick_state new_right = {0, 0, false};
bool rpc_success = transaction_rpc_exec(
RPC_GET_JOYSTICK_STATE, sizeof(joystick_state), &state_left,
sizeof(joystick_state), &new_right);
if (rpc_success) {
process_right_joystick(&new_right);
}
}
While I think this could have been made to be easier to find in the QMK docs, I appreciate how QMK is designed in a way that writing code that incorrectly uses parts of the internal API is difficult. Encoding the joystick state in the matrix would have been a weird use of the default infrastructure and the RPC approach is much more flexible and allows me to supply my own logic outside of QMK’s APIs.
To hook the joystick up to button presses, I added some nice interfaces that allows me to define an action and it’s “inverse” so I can have a virtual button “held down” when the joystick is in some location, and “released” when the joystick moves next. However, the joysticks that I have installed were pretty bad in terms of resolution, and the solution to mount them was a modest amount of hot glue. I’m not against using hot glue, but if used in large quantity, it’s hard to remove later. I’d like to be able to swap out the joysticks to try different profiles, different positions, and maybe even try some other input mechanisms besides joysticks at some point. In light of that, what I really wanted was some kind of platform that the joysticks could sit on that made replacement easy. My first approach was to try molding something that would use the slots for where a switch would have gone out of hot glue.
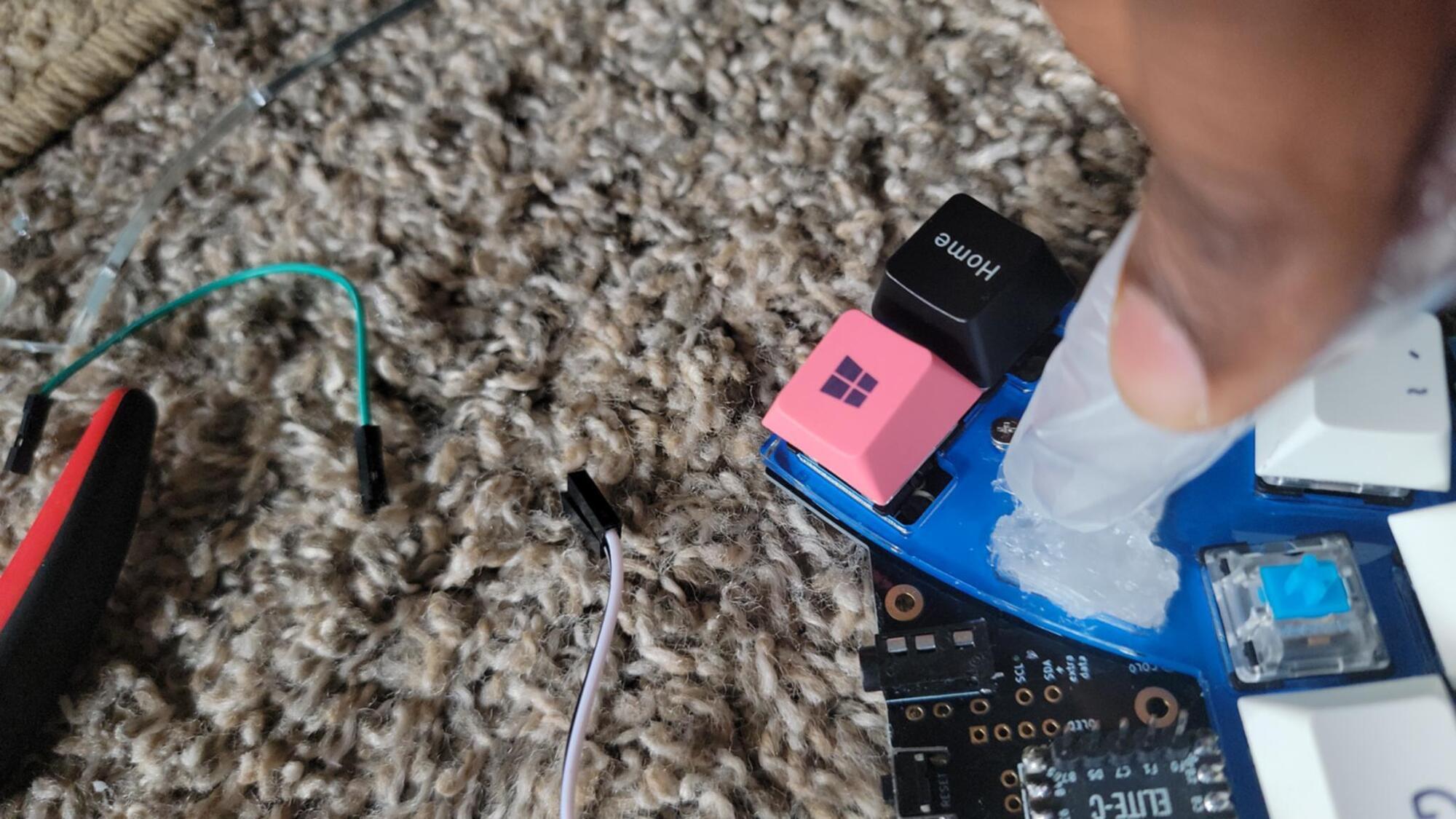
Pictured above is me trying to cure such a casting with a piece of ice in a ziploc bag. Almost needless to say, but this didn’t work at all, and was a huge, so mess. I was about to throw in the towel and resign myself to learning how to 3D print at my local library before I remembered that my brother had given me a 3D printing pen a few years ago. At the time, I didn’t really know what to do with one, and the few ideas I had quickly met the reality that using a 3D pen was a skill that I hadn’t grown yet. However, it seemed like a good tool to try using on my current problem.
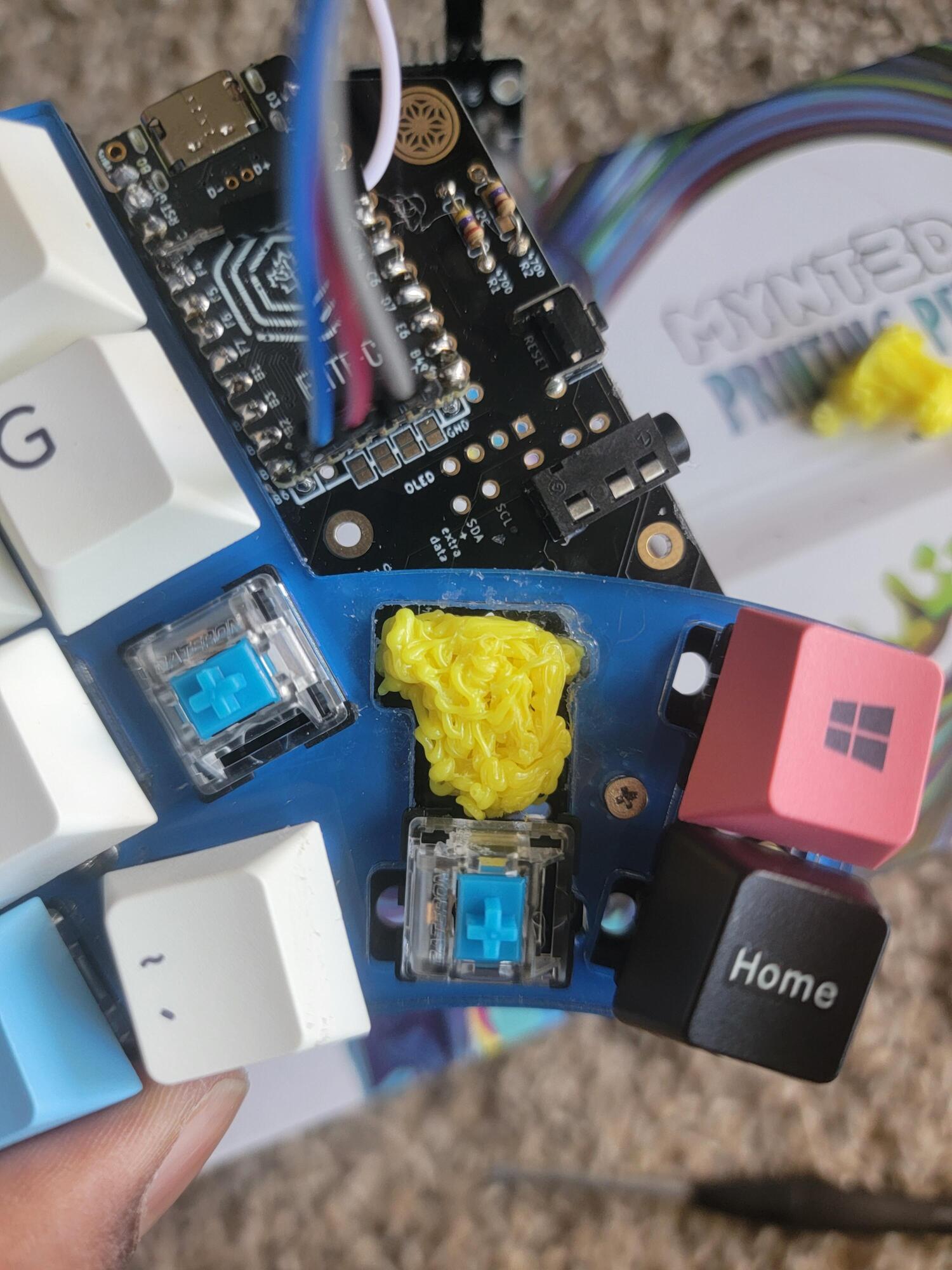
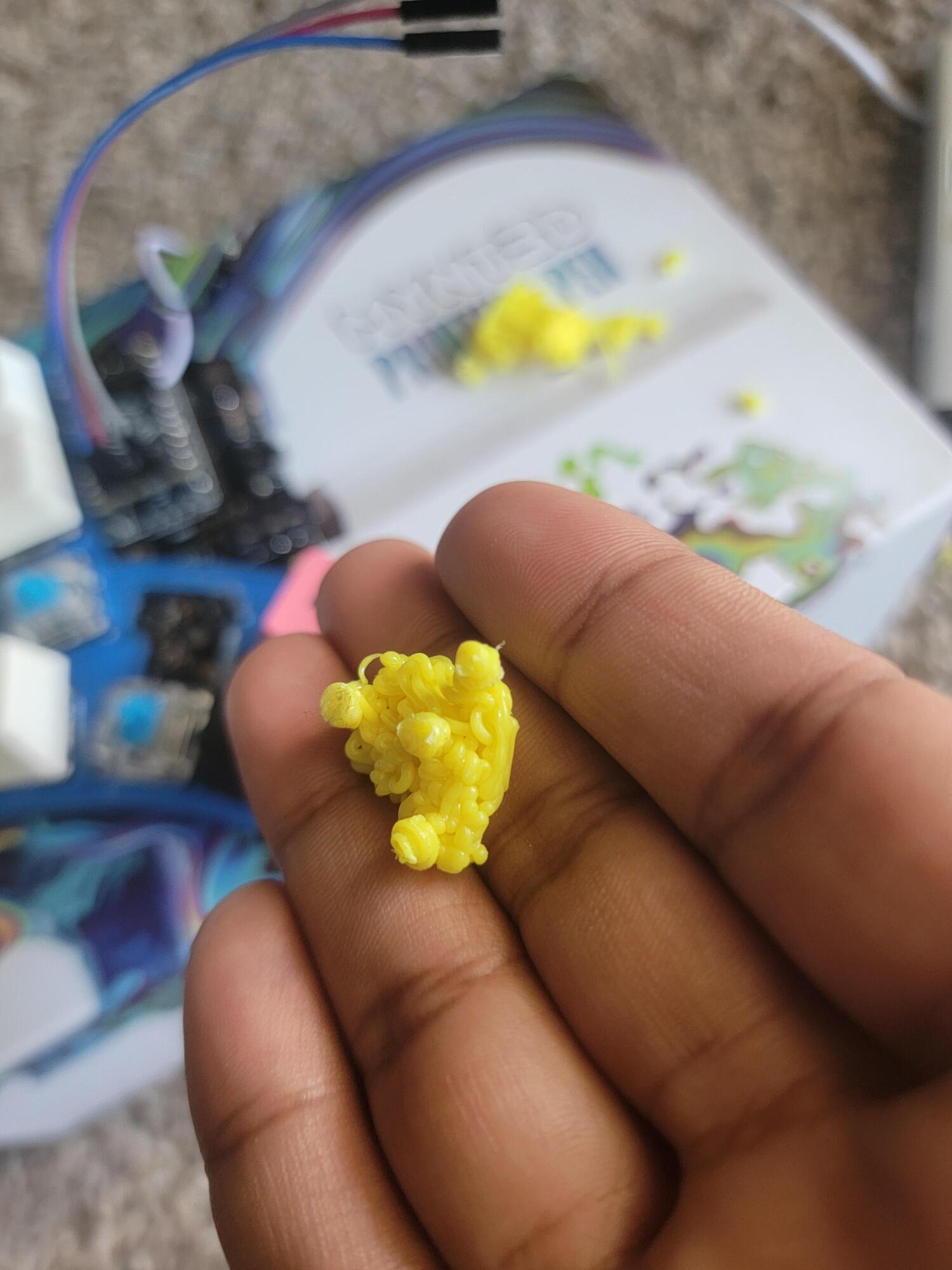
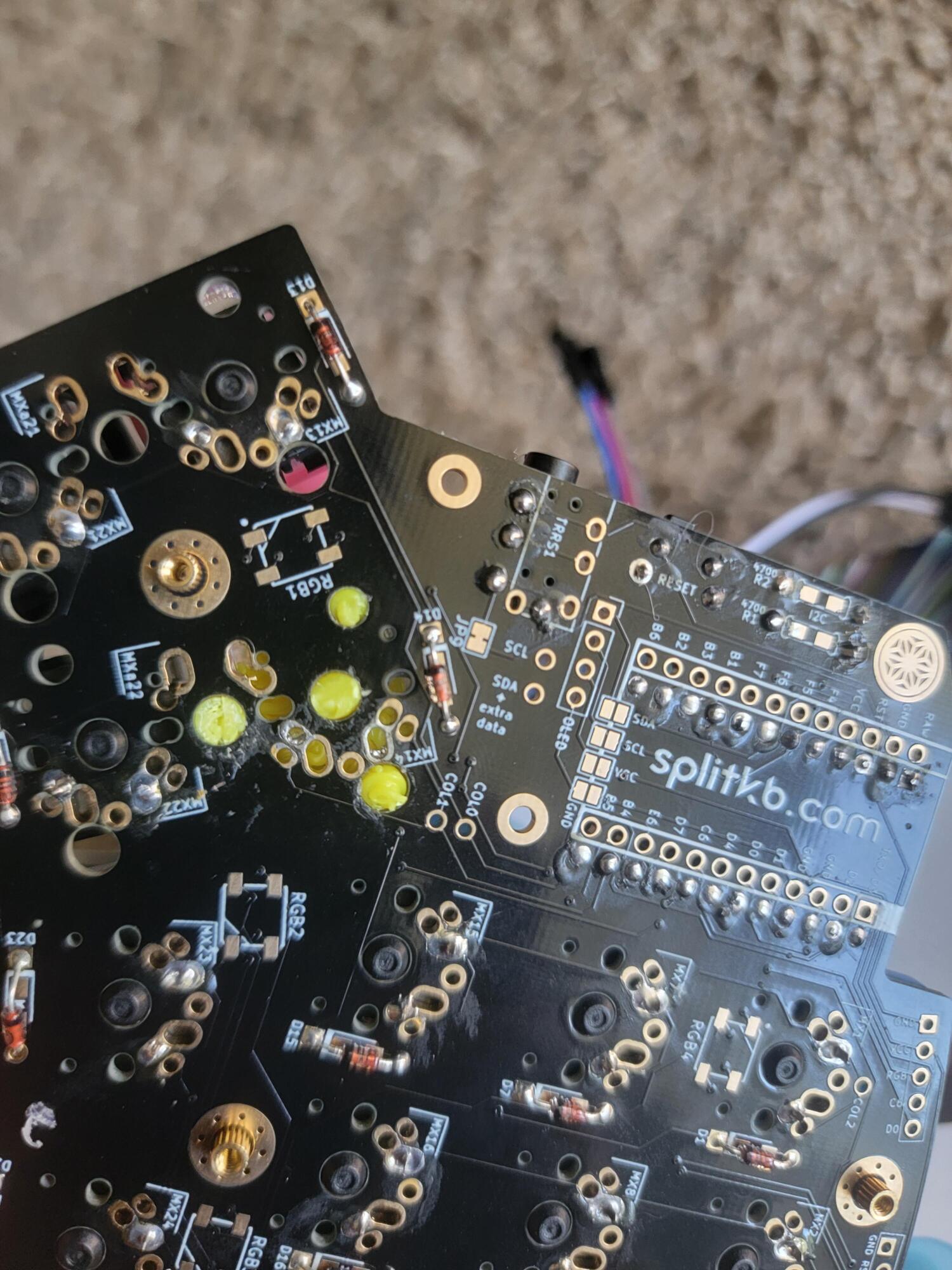
This worked better than I expected! It took a few attempts to get one I was happy with (the one pictured above is one of the early attempts), but once I had something reasonable, I swapped out the tip on my soldering iron to a flat tip that I could then smooth and cleanup the part with.
Next, I got a replacement joystick, but the PCB it came with was too large to mount in the existing assembly, so I made a small hand-wired circuit instead.
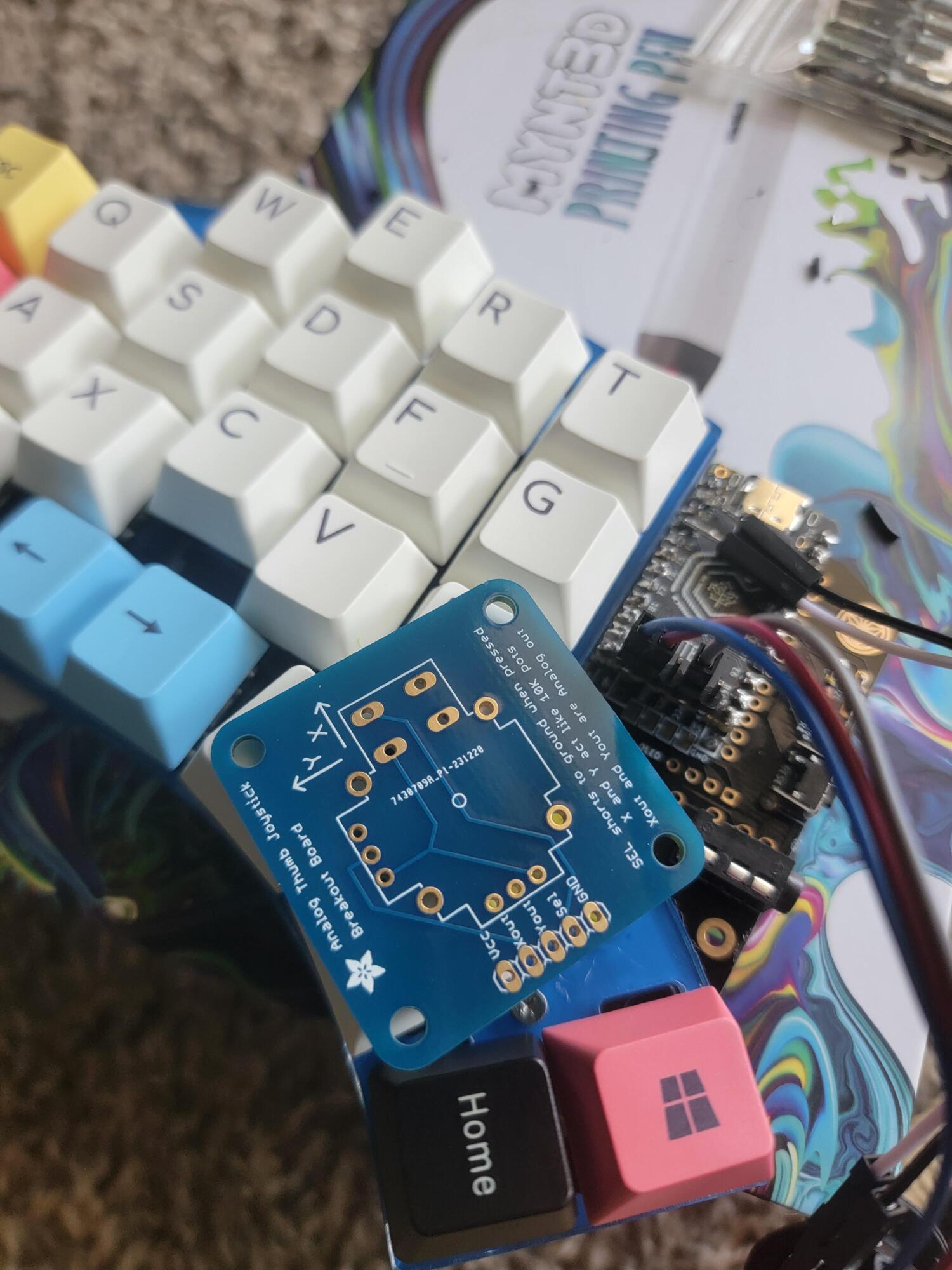
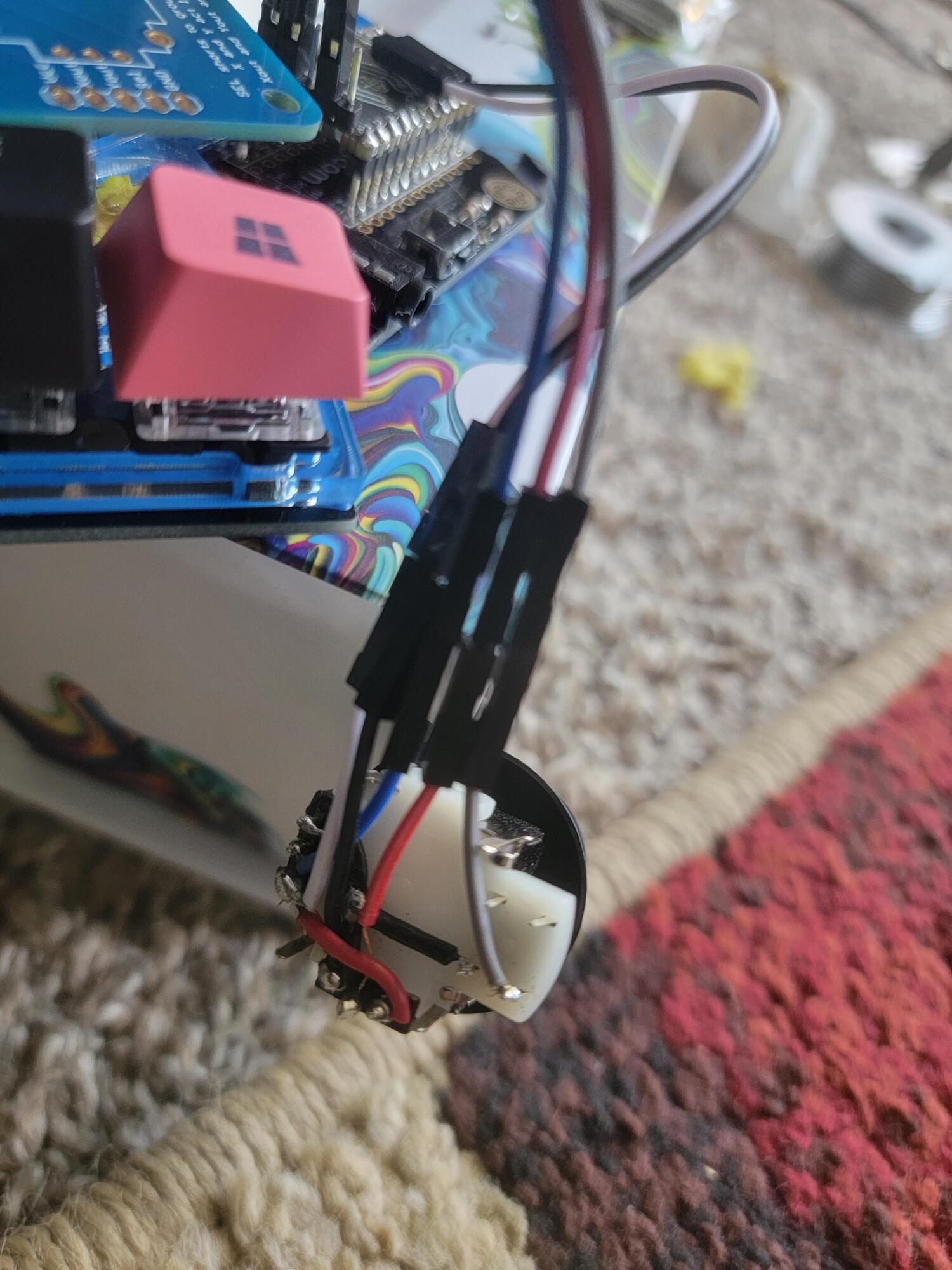
To attach the joystick to the 3D printed part, I used a bit of hot glue. However, this revealed that moving the joystick would pull the platform out of the switch slots, so I ended up adding a bit of a brace on the other side to really hold things down.
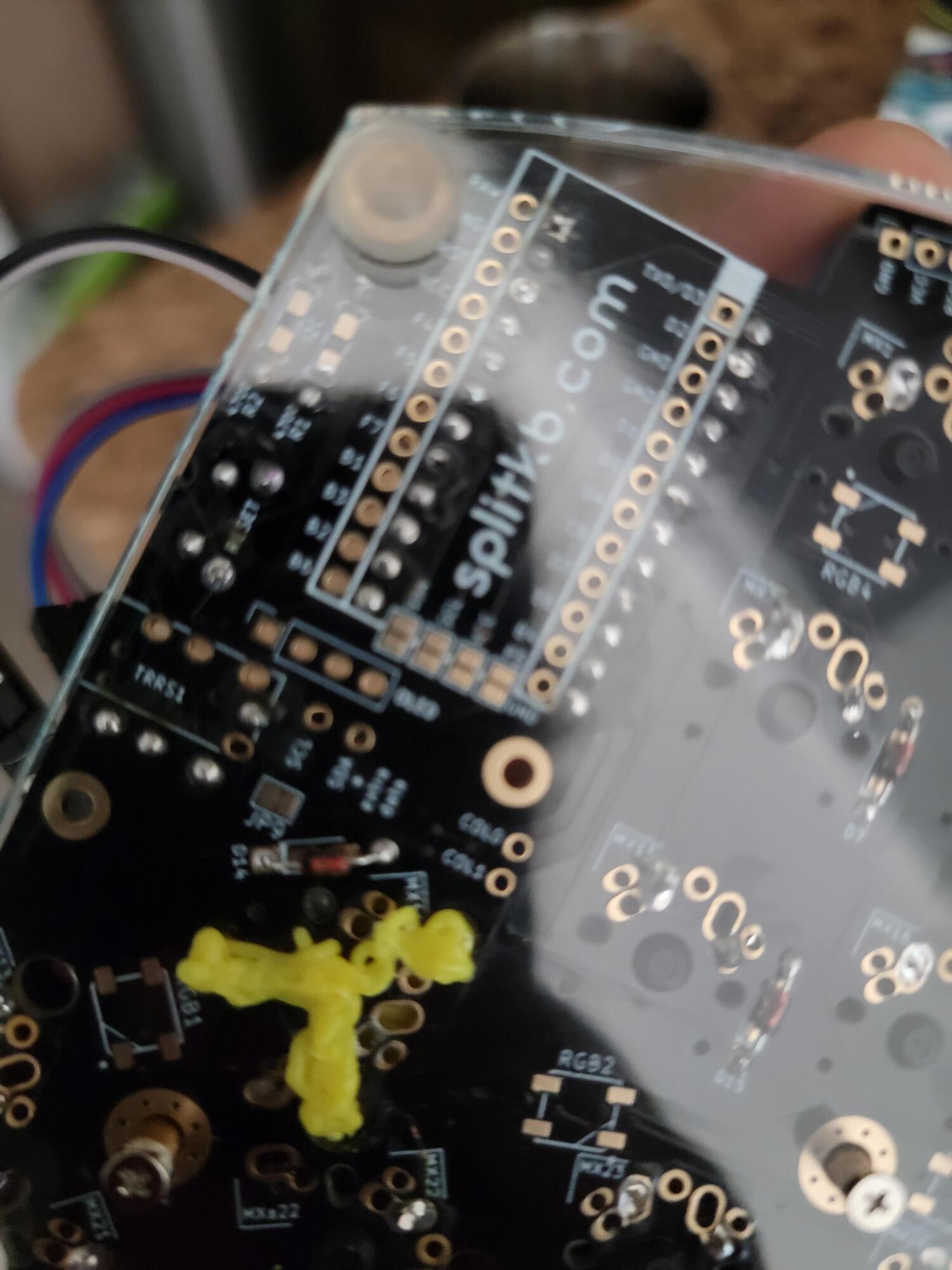
This isn’t ideal since I wanted something I could just pull out and mess around with, but it’s simple enough to remove the backplate, cut the brace, and then add the braces back when I’m ready to close things up again.
The project is really coming together! This entire post was typed exclusive on the new keybaord. I don’t really like the 3 row layout so far - when I revisit designing the layout itself, I’ll probably do a 4x6 style matrix. So far, the joysticks don’t seem super useful. This is a combination of the joystick positioning being a bit awkward, but also the joysticks not being mapping to anything super interesting. I think I’ll probably need to explore moving the joysticks further down. Having unlocked the 3D pen as a tool feels super empowering though, and I think it’ll give me greater freedom in figuring out where the joystick will live!